Material selection for beginners
A lot depends on the 3D printing material, because in most cases it determines the printing method, 3D printing quality and other important characteristics.
For example, if it is important:
- accuracy
- quality
- detail
- transparency
it is better to print with photopolymer.
The quality of the printed part will be almost perfect, but this material is less durable than thermoplastic. It is not about impact resistance, but about bending and deformation strength.
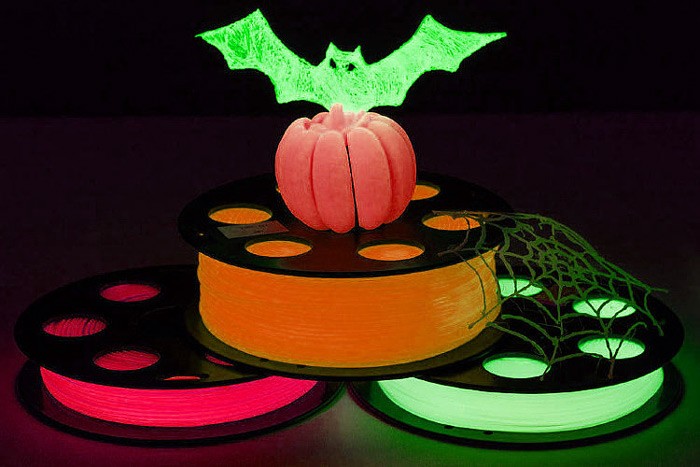
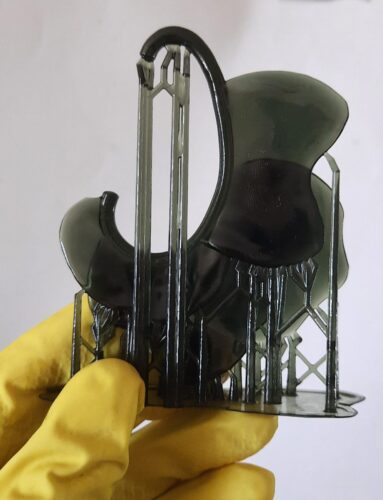
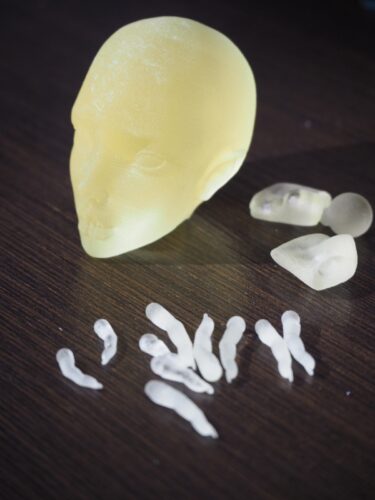
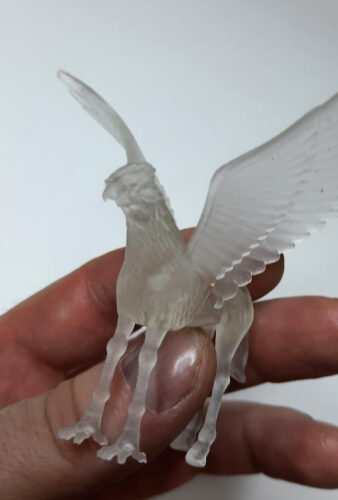
To solve these problems, ABS-Like photopolymer was created, which is closer in characteristics to ABS plastic and has greater elasticity.
If such material parameters are important as:
- strength
- elasticity
Thermoplastics are well suited for these properties.
Here are the main and most popular of them:
PLA is an organic plastic made from corn. Fully biocompatible, it can be used to print moulds for printing, children’s toys and other environmentally friendly things.
PET-G is a highly bonded plastic. Parts, especially small ones, are very strong, and the accuracy of printing dimensions is better than ABS. An example of this plastic is PET plastic bottles, which have excellent strength. PET-G is characterised by additives for durability.
ABS is a very popular plastic often used in the automotive industry and for machinery enclosures. It has excellent bending strength and a large temperature range for use.
And if you need other qualities of the material, you should choose from other types. It is better to entrust this to our specialist. Based on his extensive experience, he will suggest the best material in terms of price-quality ratio.
The table below summarises the characteristics of most 3D printing materials.
Name | ABS | PLA | PET-G | ASA | Carbon | Nylon | ABS/PC | HIPS | SBS(Watson) | PP | TPU | Flex | Gummy | Polyamide | Gypsum polymer | Base photopolymer | ABS- Like photopolymer | Flex photopolymer |
---|---|---|---|---|---|---|---|---|---|---|---|---|---|---|---|---|---|---|
Material type | Popular | Popular | Popular | Special | Heavy duty | Heavy duty | Special | Special | Special | Special | Rubber | Rubber | Rubber | Engineering | Gypsum | Ultra-precise | Ultra-precise | Ultra-precise |
Print type | FDM | FDM | FDM | FDM | FDM | FDM | FDM | FDM | FDM | FDM | FDM | FDM | FDM | SLS | CJP | SLA | SLA | SLA |
Decoding | Acrylic nitrile butadiene styrene | Poly lactide | Poly ethylene terephthalate | Acrylo nitrile styrene acrylate | Nylon with carbon fiber | Poly amide | ABS/ Polycarbonate | Impact durable polystyrene | Styrene butadiene copolymer | Poly propylene | Thermo plastic polyurethane | Thermo elasto plastic | Synthetic rubber | Amide | Gypsum | Basic | Photopolymer ABS-Like | Photopolymer Flex |
Minimum layer thickness, microns | 50 | 50 | 50 | 50 | 50 | 50 | 50 | 50 | 50 | 50 | 50 | 50 | 50 | 100 | 100 | 15 | 15 | 15 |
Accuracy, % | ± 1 | ± 0.1 | ± 2 | ± 3 | ± 1.5 | ± 2 | ± 1.5 | ± 0.5 | ± 0.4 | ± 2 | ± 2 | ± 2 | ± 2 | ± 2 | ± 0.3 | ± 0.01 | ± 0.01 | ± 0.01 |
Density, g/cm3 | 1.1 | 1.25 | 1.26 | 1.08 | 1.24 | 1.13 | 1.11 | 1.05 | 1.01 | 0.9 | 1.15 | 1.1 | 1.05 | 0.85 | 2.3 | 1.1 | 1.25 | 1.08 |
tensile tensile strength, MPa | 22 | 57 | 55 | 37 | 85 | 83 | 55 | 17 | 34 | 75 | 28 | 18 | 15 | 48 | 26 | 41 | 52 | 43 |
Modulus of elasticity at tension, MPa | 1600 | 3300 | 1730 | 1120 | 5160 | 2700 | 2850 | 930 | 1300 | 1240 | 71 | 63 | 45 | 1700 | 28 | 1779 | 2385 | 1500 |
Bending strength limit, MPa | 41 | 55 | 83 | 76 | 122 | 70 | 80 | 38 | 36 | 37 | 7 | 6 | 4 | 71 | 44 | 59-70 | 40-70 | 43 |
modulus of elasticity in bending, MPa | 2100 | 2300 | 2060 | 1350 | 5160 | 2600 | 2300 | 1350 | 1500 | 1310 | 68 | 73 | 55 | 1700 | 10680 | 1700 | 2385 | 800 |
Elongation at break, % | 6 | 3.8 | 40 | 15 | 1.8 | 300 | 10 | 65 | 250 | 4 | 617 | 600 | 920 | 5 | 0.2 | 4 | 19.7 | 60 |
Moisture absorption,% | 0.4 | 0.4 | 0.12 | 0.4 | 0.1 | 3.1 | 0.3 | 0.1 | 0.1 | 0.1 | 0.04 | 0.04 | 0.04 | 0.5-50 | 0.5-50 | 1.1 | 1.1 | 1.1 |
Melting point , °C | 175-210 | 175-180 | 222-225 | 215-220 | 240-260 | 215-220 | 230-240 | 175-210 | 190-210 | 205 | 200-210 | 200-210 | 170 | 182 | 173-178 | 300 | 300 | 300 |
Softening temperature, °C | 100 | 50 | 80 | 100 | 120 | 120 | 135 | 96 | 76 | 103 | 95 | 110 | 65 | 100 | 115 | 80 | 80 | 90 |
Operating temperature, °C | -40 +80 | -20 +40 | -40 +70 | -40 +90 | -40 +150 | -30 +120 | -30 +120 | -40 +70 | -80 +65 | -20 +80 | -35 +90 | -100 +100 | -15 +50 | -50 +100 | -10 +70 | -35 +80 | -35 +80 | -30 +65 |
Shrinkage,% | 0.8 | 0.4-0.7 | 0.1 | 0.8 | 0.4 | 4 | 0.7 | 0.4 | 0.2 | 1–3 | 0.4- 0.7 | 0.35-0.8 | 0.35-0.8 | 0.5 | 0.5 | 0.1 | 0.1 | 0.1 |
Shore hardness | D68 | D78 | D78 | D83 | D76 | D83 | D82 | D40 | D68 | D72 | A95 | D40 | D20 | D88 | D87 | D84 | D75 | D50 |
Rockwell hardness | R110 | R70-90 | R106 | R112 | R107 | R70-R90 | R116 | L79 | R118 | R30 | – | – | – | – | – | – | – | – |
Contact with food | – | + | + | – | – | + | + | + | + | + | – | – | – | + | – | – | – | – |
The same table, but with horizontal arrangement of materials by rows
Name | Material type | Print type | Decoding | Min. layer thickness, µm | Accuracy, % | Density, g/cm3 | Tensile strength, MPa | Tensile modulus of elasticity, MPa | Bending strength, MPa | Modulus of elasticity in bending, MPa | Elongation at break, % | Moisture absorption,% | Melting point, °C | Softening temperature, °C | Operating temperature, °C | Shrinkage,% | Shore hardness | Rockwell hardness | Contact with food |
---|---|---|---|---|---|---|---|---|---|---|---|---|---|---|---|---|---|---|---|
ABS | Popular | FDM | Acrylo nitrile butadiene styrene | 50 | ± 1 | 1.1 | 22 | 1600 | 41 | 2100 | 6 | 0.4 | 175-210 | 100 | -40 +80 | 0.8 | D68 | R110 | – |
PLA | Popular | FDM | Polylactide | 50 | ± 0.1 | 1.25 | 57 | 3300 | 55 | 2300 | 3.8 | 0.4 | 175-180 | 50 | -20 +40 | 0.4-0.7 | D78 | R70-90 | + |
PET-G(Relax) | Popular | FDM | Poly ethylene terephthalate | 50 | ± 2 | 1.26 | 55 | 1730 | 83 | 2060 | 40 | 0.12 | 222-225 | 80 | -40 +70 | 0.1 | D78 | R106 | + |
ASA | Special | FDM | Acrylo nitrile styrene acrylate | 50 | ± 3 | 1.08 | 37 | 1120 | 76 | 1350 | 15 | 0.4 | 215-220 | 100 | -40 +90 | 0.8 | D83 | R112 | – |
Carbon | Heavy duty | FDM | Nylon with carbon fiber | 50 | ± 1.5 | 1.24 | 85 | 5160 | 122 | 5160 | 1.8 | 0.1 | 240-260 | 120 | -40 +150 | 0.4 | D76 | R107 | – |
Nylon | Heavy duty | FDM | Polyamide | 50 | ± 2 | 1.13 | 83 | 2700 | 70 | 2600 | 300 | 3.1 | 215-220 | 120 | -30 +120 | 4 | D83 | R70-R90 | + |
ABS/PC | Special | FDM | ABS/ Polycarbonate | 50 | ± 1.5 | 1.11 | 55 | 2850 | 80 | 2300 | 10 | 0.3 | 230-240 | 135 | -30 +120 | 0.7 | D82 | R116 | + |
HIPS | Special | FDM | Impact-resistant polystyrene | 50 | ± 0.5 | 1.05 | 17 | 930 | 38 | 1350 | 65 | 0.1 | 175-210 | 96 | -40 +70 | 0.4 | D40 | L79 | + |
SBS(Watson) | Special | FDM | Styrene butadiene copolymer | 50 | ± 0.4 | 1.01 | 34 | 1300 | 36 | 1500 | 250 | 0.1 | 190-210 | 76 | -80 +65 | 0.2 | D68 | R118 | + |
PP | Special | FDM | Polypropylene | 50 | ± 2 | 0.9 | 75 | 1240 | 37 | 1310 | 4 | 0.1 | 205 | 103 | -20 +80 | 1–3 | D72 | R30 | + |
TPU | Rubber | FDM | Thermo plastic polyurethane | 50 | ± 2 | 1.15 | 28 | 71 | 7 | 68 | 617 | 0.04 | 200-210 | 95 | -35 +90 | 0.4- 0.7 | A95 | – | – |
Flex | Rubber | FDM | Thermo elastoplast | 50 | ± 2 | 1.1 | 18 | 63 | 6 | 73 | 600 | 0.04 | 200-210 | 110 | -100 +100 | 0.35-0.8 | D40 | – | – |
Gummy | Rubber | FDM | Synthetic rubber | 50 | ± 2 | 1.05 | 15 | 45 | 4 | 55 | 920 | 0.04 | 170 | 65 | -15 +50 | 0.35-0.8 | D20 | – | – |
Polyamide | Engineering | SLS | Amide | 100 | ± 2 | 0.85 | 48 | 1700 | 71 | 1700 | 5 | 0.5-50 | 182 | 100 | -50 +100 | 0.5 | D88 | – | + |
Gypsum polymer | Gypsum | CJP | Gypsum | 100 | ± 0.3 | 2.3 | 26 | 28 | 44 | 10680 | 0.2 | 0.5-50 | 173-178 | 115 | -10 +70 | 0.5 | D87 | – | – |
Base photopolymer | Ultra-precise | SLA | Basic photopolymer | 15 | ± 0.01 | 1.1 | 41 | 1779 | 59-70 | 1700 | 4 | 1.1 | 300 | 80 | -35 +80 | 0.1 | D84 | – | – |
ABS- Like photopolymer | Ultra-precise | SLA | Photopolymer ABS-Like | 15 | ± 0.01 | 1.25 | 52 | 2385 | 40-70 | 2385 | 19.7 | 1.1 | 300 | 80 | -35 +80 | 0.1 | D75 | – | – |
Flex photopolymer | Ultra-precise | SLA | Photopolymer Flex | 15 | ± 0.01 | 1.08 | 43 | 1500 | 43 | 800 | 60 | 1.1 | 300 | 90 | -30 +65 | 0.1 | D50 | – | – |
Popular plastics
The most popular plastics, suitable for most applications, they are used for children’s toys as well as gears, housings and mechanisms.
ABS is very popular because of its large temperature range and durability, while it is low cost and easy to process.
PLA is completely environmentally friendly and does not deform much when printed.
PET-G has a very high interlayer bond and can be used in the food industry.
Name | ABS | PLA | PET-G |
---|---|---|---|
Material type | Popular | Popular | Popular |
Print type | FDM | FDM | FDM |
Decoding | Acrylic nitrile butadiene styrene | Poly lactide | Poly ethylene terephthalate |
Minimum layer thickness, microns | 50 | 50 | 50 |
Accuracy, % | ± 1 | ± 0.1 | ± 2 |
Density, g/cm3 | 1.1 | 1.25 | 1.26 |
tensile tensile strength, MPa | 22 | 57 | 55 |
Modulus of elasticity at tension, MPa | 1600 | 3300 | 1730 |
Bending strength limit, MPa | 41 | 55 | 83 |
modulus of elasticity in bending, MPa | 2100 | 2300 | 2060 |
Elongation at break, % | 6 | 3.8 | 40 |
Moisture absorption,% | 0.4 | 0.4 | 0.12 |
Melting point , °C | 175-210 | 175-180 | 222-225 |
Softening temperature, °C | 100 | 50 | 80 |
Operating temperature, °C | -40 +80 | -20 +40 | -40 +70 |
Shrinkage,% | 0.8 | 0.4-0.7 | 0.1 |
Shore hardness | D68 | D78 | D78 |
Rockwell hardness | R110 | R70-90 | R106 |
Contact with food | – | + | + |
Photopolymer resin
Photopolymers are used for very high quality and precise printing, as well as for printing fully transparent parts. They are used for jewellery, 3D printing of decorative elements, souvenirs.
Base photopolymer has a low price, but it is fragile and unstable.
ABS-Like has the maximum strength among photopolymers.
Flex photopolymer is rubber-like and has excellent elasticity.
Name | ABS | PLA | PET-G | ASA | Carbon | Nylon | ABS/PC | HIPS | SBS(Watson) | PP | TPU | Flex | Gummy | Polyamide | Gypsum polymer | Base photopolymer | ABS- Like photopolymer | Flex photopolymer |
---|---|---|---|---|---|---|---|---|---|---|---|---|---|---|---|---|---|---|
Material type | Popular | Popular | Popular | Special | Heavy duty | Heavy duty | Special | Special | Special | Special | Rubber | Rubber | Rubber | Engineering | Gypsum | Ultra-precise | Ultra-precise | Ultra-precise |
Print type | FDM | FDM | FDM | FDM | FDM | FDM | FDM | FDM | FDM | FDM | FDM | FDM | FDM | SLS | CJP | SLA | SLA | SLA |
Decoding | Acrylic nitrile butadiene styrene | Poly lactide | Poly ethylene terephthalate | Acrylo nitrile styrene acrylate | Nylon with carbon fiber | Poly amide | ABS/ Polycarbonate | Impact durable polystyrene | Styrene butadiene copolymer | Poly propylene | Thermo plastic polyurethane | Thermo elasto plastic | Synthetic rubber | Amide | Gypsum | Basic | Photopolymer ABS-Like | Photopolymer Flex |
Minimum layer thickness, microns | 50 | 50 | 50 | 50 | 50 | 50 | 50 | 50 | 50 | 50 | 50 | 50 | 50 | 100 | 100 | 15 | 15 | 15 |
Accuracy, % | ± 1 | ± 0.1 | ± 2 | ± 3 | ± 1.5 | ± 2 | ± 1.5 | ± 0.5 | ± 0.4 | ± 2 | ± 2 | ± 2 | ± 2 | ± 2 | ± 0.3 | ± 0.01 | ± 0.01 | ± 0.01 |
Density, g/cm3 | 1.1 | 1.25 | 1.26 | 1.08 | 1.24 | 1.13 | 1.11 | 1.05 | 1.01 | 0.9 | 1.15 | 1.1 | 1.05 | 0.85 | 2.3 | 1.1 | 1.25 | 1.08 |
tensile tensile strength, MPa | 22 | 57 | 55 | 37 | 85 | 83 | 55 | 17 | 34 | 75 | 28 | 18 | 15 | 48 | 26 | 41 | 52 | 43 |
Modulus of elasticity at tension, MPa | 1600 | 3300 | 1730 | 1120 | 5160 | 2700 | 2850 | 930 | 1300 | 1240 | 71 | 63 | 45 | 1700 | 28 | 1779 | 2385 | 1500 |
Bending strength limit, MPa | 41 | 55 | 83 | 76 | 122 | 70 | 80 | 38 | 36 | 37 | 7 | 6 | 4 | 71 | 44 | 59-70 | 40-70 | 43 |
modulus of elasticity in bending, MPa | 2100 | 2300 | 2060 | 1350 | 5160 | 2600 | 2300 | 1350 | 1500 | 1310 | 68 | 73 | 55 | 1700 | 10680 | 1700 | 2385 | 800 |
Elongation at break, % | 6 | 3.8 | 40 | 15 | 1.8 | 300 | 10 | 65 | 250 | 4 | 617 | 600 | 920 | 5 | 0.2 | 4 | 19.7 | 60 |
Moisture absorption,% | 0.4 | 0.4 | 0.12 | 0.4 | 0.1 | 3.1 | 0.3 | 0.1 | 0.1 | 0.1 | 0.04 | 0.04 | 0.04 | 0.5-50 | 0.5-50 | 1.1 | 1.1 | 1.1 |
Melting point , °C | 175-210 | 175-180 | 222-225 | 215-220 | 240-260 | 215-220 | 230-240 | 175-210 | 190-210 | 205 | 200-210 | 200-210 | 170 | 182 | 173-178 | 300 | 300 | 300 |
Softening temperature, °C | 100 | 50 | 80 | 100 | 120 | 120 | 135 | 96 | 76 | 103 | 95 | 110 | 65 | 100 | 115 | 80 | 80 | 90 |
Operating temperature, °C | -40 +80 | -20 +40 | -40 +70 | -40 +90 | -40 +150 | -30 +120 | -30 +120 | -40 +70 | -80 +65 | -20 +80 | -35 +90 | -100 +100 | -15 +50 | -50 +100 | -10 +70 | -35 +80 | -35 +80 | -30 +65 |
Shrinkage,% | 0.8 | 0.4-0.7 | 0.1 | 0.8 | 0.4 | 4 | 0.7 | 0.4 | 0.2 | 1–3 | 0.4- 0.7 | 0.35-0.8 | 0.35-0.8 | 0.5 | 0.5 | 0.1 | 0.1 | 0.1 |
Shore hardness | D68 | D78 | D78 | D83 | D76 | D83 | D82 | D40 | D68 | D72 | A95 | D40 | D20 | D88 | D87 | D84 | D75 | D50 |
Rockwell hardness | R110 | R70-90 | R106 | R112 | R107 | R70-R90 | R116 | L79 | R118 | R30 | – | – | – | – | – | – | – | – |
Contact with food | – | + | + | – | – | + | + | + | + | + | – | – | – | + | – | – | – | – |
Durable materials
They are used for printing robust mechanisms, as well as gears and assemblies.
Carbon is a nylon with carbon fibre added, which makes it possible to print any shapes easily and easily and provides extra strength.
Nylon has increased elasticity, strength and low abrasion.
Polyamide is similar to nylon and has the same characteristics, but thanks to printing characteristics it allows printing without supports and with higher quality than traditional printing
Name | Carbon | Nylon | Polyamide |
---|---|---|---|
Material type | Heavy duty | Heavy duty | Engineering |
Print type | FDM | FDM | SLS |
Decoding | Nylon with carbon fiber | Poly amide | Amide |
Minimum layer thickness, microns | 50 | 50 | 100 |
Accuracy, % | ± 1.5 | ± 2 | ± 2 |
Density, g/cm3 | 1.24 | 1.13 | 0.85 |
tensile tensile strength, MPa | 85 | 83 | 48 |
Modulus of elasticity at tension, MPa | 5160 | 2700 | 1700 |
Bending strength limit, MPa | 122 | 70 | 71 |
modulus of elasticity in bending, MPa | 5160 | 2600 | 1700 |
Elongation at break, % | 1.8 | 300 | 5 |
Moisture absorption,% | 0.1 | 3.1 | 0.5-50 |
Melting point , °C | 240-260 | 215-220 | 182 |
Softening temperature, °C | 120 | 120 | 100 |
Operating temperature, °C | -40 +150 | -30 +120 | -50 +100 |
Shrinkage,% | 0.4 | 4 | 0.5 |
Shore hardness | D76 | D83 | D88 |
Rockwell hardness | R107 | R70-R90 | – |
Contact with food | – | + | + |
Special materials
Materials for 3D printing parts that have special properties.
For example, ASA has UV and environmental resistance, making it suitable for outdoor use.
ABS/PC has higher strength and chemical resistance than ABS.
Name | ASA | ABS/PC | HIPS | SBS(Watson) | PP | Polyamide | Gypsum polymer |
---|---|---|---|---|---|---|---|
Material type | Special | Special | Special | Special | Special | Engineering | Gypsum |
Print type | FDM | FDM | FDM | FDM | FDM | SLS | CJP |
Decoding | Acrylo nitrile styrene acrylate | ABS/ Polycarbonate | Impact durable polystyrene | Styrene butadiene copolymer | Poly propylene | Amide | Gypsum |
Minimum layer thickness, microns | 50 | 50 | 50 | 50 | 50 | 100 | 100 |
Accuracy, % | ± 3 | ± 1.5 | ± 0.5 | ± 0.4 | ± 2 | ± 2 | ± 0.3 |
Density, g/cm3 | 1.08 | 1.11 | 1.05 | 1.01 | 0.9 | 0.85 | 2.3 |
tensile tensile strength, MPa | 37 | 55 | 17 | 34 | 75 | 48 | 26 |
Modulus of elasticity at tension, MPa | 1120 | 2850 | 930 | 1300 | 1240 | 1700 | 28 |
Bending strength limit, MPa | 76 | 80 | 38 | 36 | 37 | 71 | 44 |
modulus of elasticity in bending, MPa | 1350 | 2300 | 1350 | 1500 | 1310 | 1700 | 10680 |
Elongation at break, % | 15 | 10 | 65 | 250 | 4 | 5 | 0.2 |
Moisture absorption,% | 0.4 | 0.3 | 0.1 | 0.1 | 0.1 | 0.5-50 | 0.5-50 |
Melting point , °C | 215-220 | 230-240 | 175-210 | 190-210 | 205 | 182 | 173-178 |
Softening temperature, °C | 100 | 135 | 96 | 76 | 103 | 100 | 115 |
Operating temperature, °C | -40 +90 | -30 +120 | -40 +70 | -80 +65 | -20 +80 | -50 +100 | -10 +70 |
Shrinkage,% | 0.8 | 0.7 | 0.4 | 0.2 | 1–3 | 0.5 | 0.5 |
Shore hardness | D83 | D82 | D40 | D68 | D72 | D88 | D87 |
Rockwell hardness | R112 | R116 | L79 | R118 | R30 | – | – |
Contact with food | – | + | + | + | + | + | – |
Rubber materials
Sometimes you need to print rubber things like phone case, gasket, rubber grommets and many more.
For printing gaskets and grommets, Gummy is the best choice.
If you need chemical resistance such as petrol and oil, Flex is better.
For printing of covers it is better to use Flex photopolymer, as it allows to create high-quality and transparent products.
Name | TPU | Flex | Gummy | Flex photopolymer |
---|---|---|---|---|
Material type | Rubber | Rubber | Rubber | Ultra-precise |
Print type | FDM | FDM | FDM | SLA |
Decoding | Thermo plastic polyurethane | Thermo elasto plastic | Synthetic rubber | Photopolymer Flex |
Minimum layer thickness, microns | 50 | 50 | 50 | 15 |
Accuracy, % | ± 2 | ± 2 | ± 2 | ± 0.01 |
Density, g/cm3 | 1.15 | 1.1 | 1.05 | 1.08 |
tensile tensile strength, MPa | 28 | 18 | 15 | 43 |
Modulus of elasticity at tension, MPa | 71 | 63 | 45 | 1500 |
Bending strength limit, MPa | 7 | 6 | 4 | 43 |
modulus of elasticity in bending, MPa | 68 | 73 | 55 | 800 |
Elongation at break, % | 617 | 600 | 920 | 60 |
Moisture absorption,% | 0.04 | 0.04 | 0.04 | 1.1 |
Melting point , °C | 200-210 | 200-210 | 170 | 300 |
Softening temperature, °C | 95 | 110 | 65 | 90 |
Operating temperature, °C | -35 +90 | -100 +100 | -15 +50 | -30 +65 |
Shrinkage,% | 0.4- 0.7 | 0.35-0.8 | 0.35-0.8 | 0.1 |
Shore hardness | A95 | D40 | D20 | D50 |
Rockwell hardness | – | – | – | – |
Contact with food | – | – | – | – |